Using Aircraft Expertise for Underwater Operations
Regional Cabled Array (RCA) Engineer Eric McRae came to the RCA Team with a 20+ year background keeping aircraft in the air, cars on the road, and medical devices safe. McRae worked on a Head-Up display and skid control and braking systems on some large commercial aircraft that are flying now. He also worked on a popular pacemaker/defibrillator for a medical instrument company. As a result of this experience, and long-term work in automotive engine control, McRae brought with him a mindset about correct behavior of control software to the RCA. He simply will not accept anything that is misbehaving. In the past, people’s lives were at stake, now it’s possible interruption of data collection or loss of scientific equipment.
McRae adopted his approach to help design and keep operational the Shallow Profilers on the RCA moorings which must work correctly for a year at a time in the cold, dynamic, and sometimes hostile, waters of the Pacific Ocean. The Shallow Profiler houses 10 scientific instruments and includes a winch that pays out power and communication cable allowing the science pod to rise through the water column to a depth below the surface determined by currents and wave conditions.
“I think that the Cabled Array Team is successful because many of us came from industries where it was not acceptable to produce something that could fail,” McRae explained. “We use this same mindset to figure out ways to make things work and keep them working even under the most difficult of circumstances.”
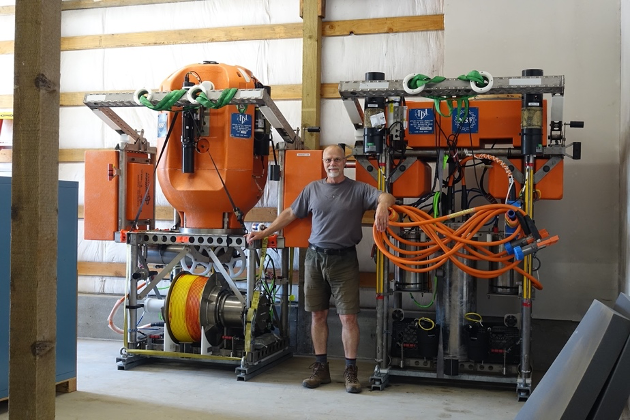
From his first days at the RCA, Gary Harkins, his boss at the time, told McRae that his job was to make sure the Shallow Profiler was safe. “Safety was the top priority — not science, or anything else. Once we were sure the profiler could be operated safely, we could accomplish whatever the science mission wanted.” Initially, McRae worked with Dr. Doug Luther and Dr. Kendra Daly to understand how the science team wanted the profiler to run. Once he understood the science requirements, he worked with RCA’s mechanical designers to understand how they wanted to design the mechanical aspects of the system.
McRae then used his experience to influence the design and created a viable electronic control system that supports communications that keep the winch running and its science pod node traveling up towards the surface and back down nine times a day. A winched cable provides continuous power and communications to the science pod, allowing science and engineering data to flow to shore in real time. The mechanical design and control system have kept the Shallow Profiler operational since its launch in 2014.
The control system continually “talks” to the winch and science pod to assess movement through the water. Near the bottom, the science pod doesn’t move very much, except for an occasional tilt caused by currents. As it gets close to the surface, however, surface waves can have a huge impact on how the profiler moves and how much tension is on the cable. The science pod weighs ~900 pounds in air so when it gets moving back and forth underneath waves, it could significantly stress the cable. To prevent this from happening, the science pod “reports” three times a second to the control system about the conditions it is experiencing. These reports include acceleration, rotation, proximity to the surface, wave length, and a slew of other variables so that needed adjustments can be made automatically to keep the winch and ultimately its valuable science pod “safe.” If conditions warrant, the control system has the capability of aborting a running profile and/or parking the science pod near the mooring to wait things out.
The Shallow Profiler is often on the move. Each of the nine daily profiles take between one and a half to two and a half hours, depending on the profile type and ocean conditions. There’s a gap of about 30 to 45 minutes between profiles, where the science pod is parked down near the mooring platform. During that time, the controller is constantly monitoring the waves on the surface. McRae developed an algorithm to look at the worst-case peak to trough wave pressure so that when the profiler starts up for a run towards the surface, it has already calculated what it thinks the worst wave height combination will be. The original requirements of the system were that the science pod can go no closer to the surface than five meters or three wave heights, whichever is greater, so when it starts up, it already knows the ceiling for the coming profile.
“As designed, the profiler is smarter than we are. It makes seven decisions three times a second to ensure that it is on the right path and has accounted for all predictable conditions” McRae said.
Of course, there are other hazards besides ocean conditions. In September of 2017, a trawler’s net hit the mooring line at the Oregon Offshore site and eventually the mooring platform itself, pulling the 14,000-pound mooring and its two huge anchors from the seafloor. The profiler was running at the time and recorded the action until the boat pulled hard enough that the seafloor cable came unplugged. There has also been a smattering of mechanical issues, but the system has matured nicely. Should something unexpected go wrong in the future, McRae has programmed the profiler to take “evasive” action, then notify him and his team on land. This performance record demonstrates that not only did McRae’s work help keep the profiler safe, it helped make it a reliable component of the RCA that scans through the water with ease. The three profilers have made >40,000 profiles since 2015, making unprecedented measurements of ocean parameters.