Battling the Corrosive Properties of Seawater
OOI engineers face the challenge of keeping ocean observing equipment operational in demanding locations for up to a year at a time. In addition to wind, waves, extreme pressure, ship traffic and trawling disruption, engineers continually battle the corrosive properties of salt water.
Senior Technician for OOI’s Coastal Endurance Array Kristin Politano provided a primer on OOI’s tactics to prevent corrosion of its equipment and instrumentation. “It’s a fun balancing act between cost versus strength versus weight versus durability. Different metals are great for certain things, so we use them in different places.”
OOI engineers try to avoid all forms of corrosion, especially galvanic corrosion, an electrochemical process where one metal corrodes preferentially in the presence of an electrolyte. In this case, seawater serves as the electrolyte or the corrosion “enabler.” When two dissimilar metals are connected in seawater, one of them is going to corrode faster than the other.
Since zinc is very prone to corrosion and corrodes much faster than other materials used on OOI moorings, engineers use it as a “sacrificial lamb” in OOI operations. They place zinc strategically on the moorings to encourage galvanic corrosion to occur on the zinc, rather than degrading instruments, electronics, and the frames that hold the moorings and instrumentation in place.
Politano gave an example of how zinc works to protect other metals used on the moorings. Aluminum is used on the Coastal Surface Piercing Profiler frames (CSPP), the Near-Surface Instrument Frames (NSIF), a cage that contains ocean observing instruments below surface moorings, and Multi-function Nodes (MFN) frames, which are at the base of some surface moorings and act both as anchors as well as platforms to affix instruments.
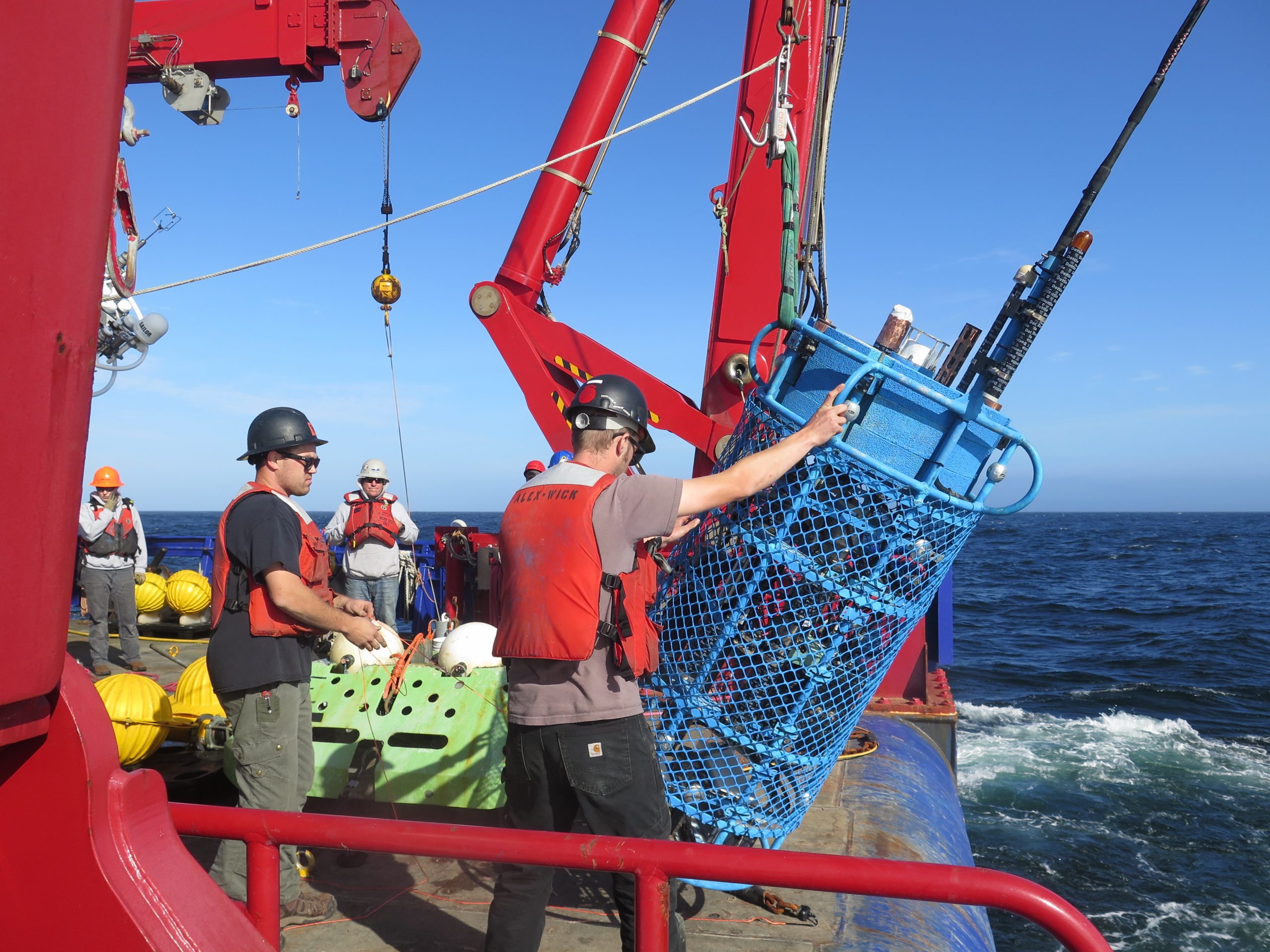
The NSIF, MFN, and CSPP have sacrificial zinc cylinders attached so that when the frames containing the instruments go into the water, the aluminum doesn’t degrade as quickly as it might otherwise. The zinc will degrade first, providing a protective layer for the important assets within the frames. “Zinc serves as a really effective form of galvanic corrosion protection,” Politano added. “Zincs come in many different form factors, but we use ones that can be bolted directly to the mooring frames and other mechanical components,” said Politano.
Location Dictates Effectiveness
Zincs are used on both the Coastal Endurance’s inshore and offshore mooring platforms. The zincs on the inshore platforms dissolve faster and require replacement more often due to low dissolved oxygen conditions and that encourage corrosion. Zincs on the offshore moorings last longer due to a higher oxygenated environment offshore.
Decisions about materials to use on various parts of the moorings also in part, depends on durability, conditions, and cost. Stainless steel is very durable and reacts to form a protective oxide film on its outer surface, but this reaction needs oxygen to grow and repair itself. In areas with hypoxia (lack of oxygen) particularly in the summer months, there is not enough oxygen in the water column for the stainless oxide layer to rebuild and repair itself.
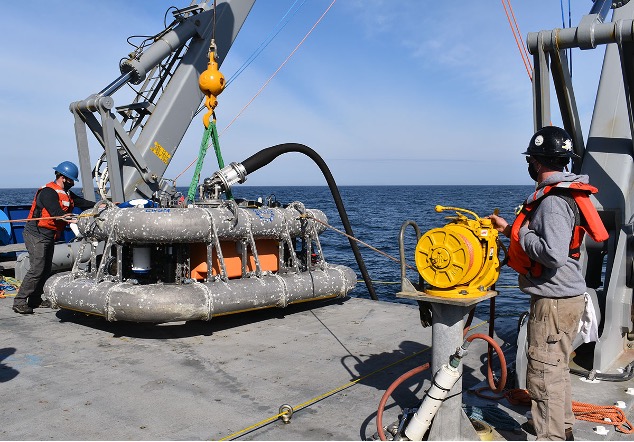
Delrin, a high-grade plastic (acetyl resin), is also used on the moorings as a corrosion preventive measure. Because of Delrin’s durability, stiffness, light weight, and water resistance, Delrin is used in instrument housings and electrical panels because it doesn’t conduct electricity, but it lacks the strength of aluminum. “Delrin is strong, but not as strong as aluminum. So, we wouldn’t make a mooring tower or a mooring Halo out of a plastic material,” said Politano. Components above water are made from aluminum because it is lightweight and extremely strong. To increase strength and resilience, above water aluminum components are powder coated that prevents water from contacting the metal. The powder coating contains various pigments, polymer resins, curatives, leveling agents, and other additives, which is applied to an aluminum surface with an electrostatic spray. “The powder coating is sprayed on, and cured in an oven that triggers a chemical reaction that hardens the coating, making a hard shell, protecting the metal beneath it,” she explained. “A good way to imagine it is like a big M&M covering the chocolate metal inside,” she added.
The OOI team uses silicon bronze (bronze coated with a silica coating) and titanium for many underwater components. The silicon bronze has mild anti-fouling properties, which is important for OOI’s coastal arrays to help reduce biofouling. The mooring components go from a bright coppery color to a green, blue patina color. The patina acts as a durable, strong, protective layer that is highly resistant to corrosion and doesn’t fatigue. “We use silicon bronze to bolt instrument clamps to MFN and NSIF frames and to attach instrument to the frames. The benefit of silicon bronze is that it is much cheaper than some of the other materials like titanium, so we can afford to use it many places,” said Politano.
Balancing Cost and Placement Considerations
Titanium is a fantastic material to use in the marine environment because it is highly corrosion resistance, very strong, and can remain in a marine environment for a long time. The downside is that it is very expensive, so it is used judiciously. Titanium also has a high strength to weight ratio, which makes it ideal for floating things in the water column and it is used to bolt together all of the critical structural mooring components. For instance, titanium bolts are used to connect surface buoys to the electromechanical chain (EM), which contains electrical components allowing power and communication with the below surface elements, to the NSIF and stretch hoses to the MFN, which anchors the mooring on the sea floor. Like stainless steel, titanium has a protective oxide layer with the ability to “heal itself.”
In addition to strength, durability, and cost the OOI team must consider the mix of materials it uses, avoiding places where two metals might touch each other. For example, copper is used as a primary anti-fouling material to mitigate the ever-present challenge of minimizing marine growth. Copper is soft so it isn’t used to attach critical mooring components. Care must be taken to avoid any dissimilar metals coming in contact with one another. The outcome of such contact would be an extreme case of galvanic corrosion!
“It really is this sort of ballet of trying to balance the cost of the material versus the strength of the material versus the weight. We put lightweight materials above the water. The expensive materials that are really strong are used to hold the whole mooring together. And then the in-between materials that are strong, but not as expensive as the really strong materials, are used to hold all the instruments together. So, it’s a fun little balancing act,” Politano concluded.
As it turns out choosing the right materials also is a good return on investment. According to OOI Lead Systems Engineer Matthew Palanza, “While the cost of these corrosion-prevention materials is high, the loss of equipment and data due to failures caused by corrosion is much greater. Incorporating corrosion-prevention materials into the array extends their service life much longer. This makes it possible for some housings, connectors, and other components to be re-used every time an array is redeployed. In fact, some housings are designed to last for the 30-year duration of the program.”